Oxide Zinc Powder in Industry: Properties, Processing, and Performance
Oxide zinc powder, a fine, white or grayish substance, plays a critical role in many industrial sectors—from rubber production to ceramics, pharmaceuticals, electronics, and more. Thanks to its unique physicochemical properties and broad functionality, zinc oxide (ZnO) in powder form is a go-to material for manufacturers looking to enhance durability, stability, and performance.
In this article, we’ll explore the core properties, processing methods, and real-world applications of oxide zinc powder, especially in industrial manufacturing.
🔍What Is Oxide Zinc Powder?
Oxide zinc powder refers to finely milled zinc oxide (ZnO), a chemical compound consisting of zinc and oxygen atoms in a 1:1 ratio. This white powder is widely used across various industrial and commercial applications due to its unique chemical and physical properties.
Chemical and Physical Characteristics:
-
Molecular Formula: ZnO
-
Appearance: A fine white powder, with particle sizes ranging from nanometers to micrometers depending on the milling process and application requirements.
-
Melting Point: Approximately 1975 °C, making it highly thermally stable.
-
Solubility: Zinc oxide powder is insoluble in water, which contributes to its stability in many products, but it can dissolve in acidic and alkaline solutions, allowing for chemical reactivity in controlled environments.
-
Refractive Index: Around 2.0, making ZnO an excellent material in optical coatings and UV-blocking applications.
-
Bandgap Energy: Approximately 3.3 eV, which classifies it as a wide-bandgap semiconductor. This property is crucial for its role in optoelectronics, UV sensors, and photovoltaic devices.
Production Processes:
Oxide zinc powder is typically produced via two main industrial methods, each influencing the purity and particle characteristics:
-
Direct Process (American Process):
-
Involves roasting metallic zinc in air to form zinc oxide.
-
Produces a relatively pure form of ZnO suitable for many industrial uses.
-
-
Indirect Process (French Process):
-
Starts by vaporizing zinc metal, which is then oxidized and condensed to form fine ZnO particles.
-
Results in higher purity oxide zinc powder often used in sensitive applications like pharmaceuticals and cosmetics.
-
Applications:
Due to its versatile properties, oxide zinc powder is used in a wide array of industries:
-
Rubber Industry: Serves as an activator in vulcanization, improving elasticity and durability of rubber products.
-
Cosmetics: Used in sunscreens and ointments for UV protection and skin soothing effects.
-
Electronics & Optoelectronics: Integral in manufacturing LEDs, solar cells, and sensors because of its semiconducting and optical properties.
-
Ceramics & Paints: Acts as a white pigment and provides mildew resistance.
-
Pharmaceuticals: Used in topical creams and powders for its antibacterial and healing properties.
🧬 Key Properties of Oxide Zinc Powder
Property | Industrial Relevance |
---|---|
High thermal stability | Ideal for high-temperature applications (e.g., rubber vulcanization) |
UV-blocking capability | Used in paints, coatings, and sunscreens |
Antibacterial action | Applied in cosmetics, hygiene products, and food packaging |
Electrical conductivity | Enables use in varistors, semiconductors, and batteries |
Catalytic activity | Supports chemical synthesis, petrochemical refining |
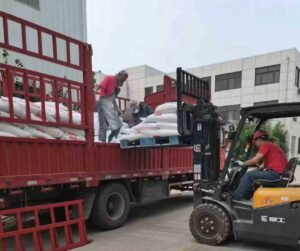
Zinc oxide’s particle size distribution, surface area, and purity significantly affect its performance in each application.
⚙️
How Is Oxide Zinc Powder Processed?
The industrial processing of oxide zinc powder is a carefully controlled sequence of steps designed to achieve the desired purity, particle size, and surface characteristics, depending on its final application. Each stage plays a vital role in ensuring consistent quality and performance.
1. Raw Material Selection
The process begins with choosing the appropriate raw materials:
-
Metallic Zinc: Often used when ultra-high purity is required.
-
Zinc Ore (Zincite): Naturally occurring zinc oxide mineral, used for large-scale industrial production.
The purity level of the raw material typically ranges from 99.5% to 99.9%, influencing the quality of the final oxide zinc powder product.
2. Production Methods
There are two primary industrial production methods, each with distinct advantages:
-
Indirect (French) Process:
In this method, metallic zinc is first vaporized at high temperatures. The zinc vapor is then oxidized by exposure to air or oxygen, resulting in the formation of very fine, high-purity zinc oxide powder. This process allows precise control over particle size and morphology, making it ideal for applications such as pharmaceuticals, cosmetics, and high-tech electronics where purity and particle characteristics are critical. -
Direct (American) Process:
This method involves roasting zinc ores (such as zinc sulfide concentrates) with carbon in a furnace. The chemical reaction reduces the ores and produces zinc vapor, which is then oxidized to form zinc oxide powder. This process is more economical and widely used for producing industrial-grade zinc oxide for rubber, ceramics, and paints where ultra-high purity is less critical but cost efficiency is important.
📖 Learn more via: AZoM Zinc Oxide Overview (link for reference)
3. Post-Treatment
Once the zinc oxide powder is synthesized, it often undergoes several post-processing steps to tailor its properties for specific uses:
-
Micronization: Mechanical milling to achieve uniform particle size distribution, important for consistent performance in rubber compounding and coatings.
-
Surface Modification: Chemical or physical treatments applied to alter the surface properties, such as adding hydrophobic coatings to improve dispersion in rubber or polymers.
-
Coating: Sometimes zinc oxide particles are coated with stearic acid or other agents to enhance compatibility with various matrices, improving stability and processing behavior.
4. Packaging & Storage
Proper packaging and storage are crucial to maintaining product quality:
-
Packaging: Zinc oxide powder is typically packed in 25 kg paper bags with inner polyethylene liners or in large 1-ton bulk sacks for industrial clients.
-
Storage Conditions: The powder must be kept in a dry, cool environment to prevent moisture absorption, which can cause clumping or degradation of properties. Proper handling avoids contamination and preserves the powder’s fine particle structure.
🏭
Industrial Applications of Oxide Zinc Powder
Oxide zinc powder (ZnO) is a highly versatile material widely used across many industries thanks to its unique chemical and physical properties. Below are some of the major industrial applications that highlight its critical role in modern manufacturing and technology.
✔️ 1. Rubber & Tire Manufacturing
The rubber industry is one of the largest consumers of oxide zinc powder. Zinc oxide plays several vital roles in rubber production:
-
Activator in Sulfur Vulcanization: ZnO acts as an activator by accelerating the vulcanization process, which crosslinks rubber polymers to improve elasticity, resilience, and durability.
-
UV Protector: It protects rubber products like tires from UV degradation, prolonging their lifespan when exposed to sunlight.
-
Reinforcement Agent: Enhances the mechanical strength and abrasion resistance of tires and rubber goods by improving crosslink density.
📘 According to the Rubber Chemistry and Technology Journal, zinc oxide significantly increases crosslink densityand improves elongation resistance, contributing to stronger and more flexible rubber products.
✔️ 2. Ceramics and Glass
In the ceramics and glass industries, zinc oxide is valued for improving both functional and aesthetic qualities:
-
Thermal Shock Resistance: ZnO helps ceramics withstand rapid temperature changes, reducing cracking and damage during firing or use.
-
Gloss and Whiteness: Adds brilliance and enhances the whiteness of ceramic glazes and glass finishes, resulting in more visually appealing products.
-
Melting Point Control: Modifies the melting behavior of ceramic frits and enamels, enabling better processing and surface smoothness.
Zinc oxide is widely used in frits, enamels, and ceramic glazes, where it acts as both a flux and stabilizer.
✔️ 3. Electronics & Semiconductors
Due to its semiconducting and optical properties, oxide zinc powder is a key material in several advanced electronic applications:
-
Varistors: Used in voltage-dependent resistors to protect circuits from voltage spikes. ZnO-based varistors offer fast response and high energy absorption.
-
Transparent Conductive Oxide (TCO) Layers: ZnO films provide transparency and conductivity, essential in displays, solar cells, and touchscreens.
-
Thin-Film Transistors and Sensors: Utilized in gas sensors, UV detectors, and photodetectors due to its wide bandgap and sensitivity to environmental changes.
✔️ 4. Paints and Coatings
In the paints and coatings industry, zinc oxide contributes to both durability and aesthetics:
-
UV Resistance: ZnO protects paint layers from ultraviolet light damage, extending the life of outdoor coatings.
-
Mildew Prevention: Its antimicrobial properties help prevent mildew and fungal growth on painted surfaces.
-
Whiteness and Opacity: Acts as a white pigment, enhancing brightness and hiding power in paints.
🌐 For more detailed information, see: ScienceDirect — Zinc Oxide in Coatings
✔️ 5. Pharmaceuticals and Cosmetics
Oxide zinc powder is widely used in healthcare and personal care products:
-
Sunscreens: Micronized or nano-sized ZnO blocks both UV-A and UV-B rays, providing broad-spectrum sun protection while being gentle on the skin.
-
Wound Healing Creams: ZnO promotes skin regeneration and acts as a protective barrier for minor cuts and burns.
-
Antiseptic and Anti-Inflammatory Agent: Exhibits antibacterial properties that help prevent infection and reduce inflammation in topical formulations.
🌱 Environmental & Safety Considerations
While oxide zinc powder is considered safe under normal industrial use, proper handling is essential:
-
Avoid inhalation of fine powder
-
Use PPE (masks, gloves)
-
Ensure dust control in high-volume processes
🌍 The European Chemicals Agency (ECHA) classifies ZnO as low toxicity but recommends responsible disposal and safe usage practices.
📈 Market Demand and Outlook
Global demand for zinc oxide powder is projected to reach USD 5.5 billion by 2027, driven by:
-
Growth in the automotive and tire industry
-
Expansion of electronics manufacturing
-
Rising demand for eco-friendly paints and coatings
-
Increasing use of antibacterial packaging
Major producers include Zochem, EverZinc, Umicore Zinc Chemicals, and emerging suppliers in China, India, and Southeast Asia.
❓ Frequently Asked Questions (FAQ)
Q1: What is the difference between nano zinc oxide and standard oxide zinc powder?
A: Nano ZnO has smaller particle sizes (10–100 nm), offering better dispersion, higher UV blocking, and improved reactivity—especially in cosmetics and coatings.
Q2: Is zinc oxide powder safe for skin use?
A: Yes, when produced and processed to cosmetic-grade standards, it is safe and widely used in sunscreens and baby products.
Q3: How does oxide zinc powder improve rubber performance?
A: It accelerates vulcanization, enhances elasticity, and increases tensile strength and heat resistance.
Q4: Can oxide zinc be recycled?
A: Yes. Industrial recovery systems capture and recycle ZnO from rubber pyrolysis, battery scrap, and furnace dust.
✅ Conclusion
Oxide zinc powder stands as a foundational material across multiple industries due to its thermal stability, UV resistance, and chemical versatility. Whether improving the quality of tires, ceramics, electronics, or coatings, its role in boosting product performance, durability, and safety is undeniable.
As industries evolve toward greener, smarter, and more efficient materials, oxide zinc powder will remain a key contributor to innovation and growth.